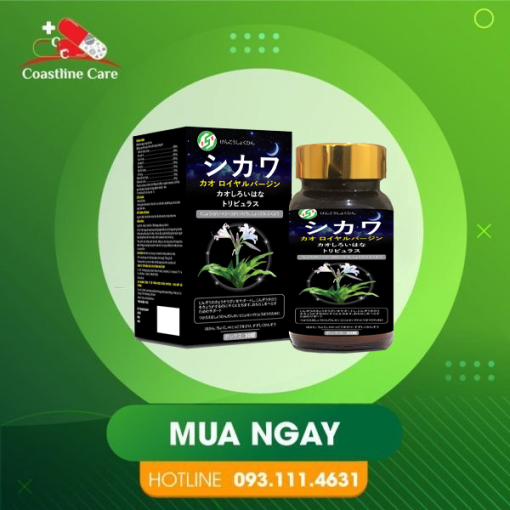
The six M's Ishikawa Diagram Each and every of the "bones" or "ribs" in the typical Ishikawa diagram signifies an issue related to good quality control, and will be explained via the six "M"s, wherever failures or prospective failures may be determined and rectified. These are definitely:
They are named right after Japanese engineering professor Kaoru Ishikawa while in the 1960s, who served apply them to manufacturing procedures.
Mother Nature - Generally uncontrollable environmental variables like fireplace or negative weather, but specific security measures can be undertaken, and insurance plan ordered for destruction or catastrophe
Prevalent works by using in the Ishikawa diagram are item style and good quality defect avoidance to recognize possible aspects resulting in an All round effect.
The lights may be a contributing bring about, nonetheless it should not be the first 1 investigated. The Ishikawa diagram should be expanded each time 5 Whys is made use of. As an example, the branch may finish up as material → component not put in → employee skipped operation → operate surroundings much too dim → lousy lights nha thuoc tay → mild bulbs burned out.
When you have sorted and prioritized your possible causes, it truly is time to start screening them to determine Should they be root triggers. Trying to see what could be the possible results in can be Shikawa achieved in many means:
Measurement - Are ways of measurement and Regulate right and precise. Do they have to be modified?
Ensure that Absolutely everyone on your team understands the condition in the exact same way. Use an issue assertion making sure that everyone seems to be on a similar page.
There can be quite a hazard of concentrating too seriously on specific components instead of taking into consideration how they may connect with one another.
También puede ser recomendable complementarlo con otras herramientas de control de calidad, por ejemplo hojas de chequeo para la recolección de datos relevantes que permitan hacer mejores análisis de causas.
The 6Ms inside the Ishikawa diagram are crucial things accustomed to recognize and analyze problems in a very program. These elements nha thuoc tay involve:
Những đối tượng sau nên thận trọng khi dùng Shikawa: Người bị bí tiểu do bị chật hẹp đường tiết niệu.
In this example, the usage of five Whys led into the true cause of the failure – the light bulbs burned out. Had the 5 Whys not been used, then the employee might have already been retrained, but precisely the same personnel or any person else can have built a similar or another mistake due to the bad lighting.
Su creador, Kaoru Ishikawa recomendaba que la espina de pescado se desarrollara hasta el quinto nivel de causas.